Plant Upgrade for Ecopro
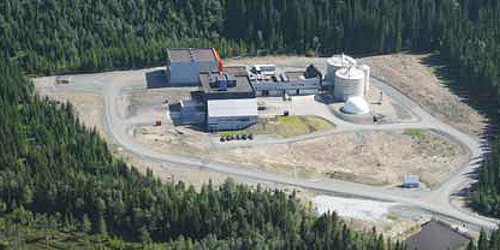
Estimated savings are € 300 000 annually at the Ecopro AD biogas plant in Verdal, Norway.
Installation of the BioPrePlant® System has reduced Ecopro’s cost for incineration significantly.
• Increased capacity from 2 to 9 tonnes per hour
• Reduced reject volume from 250 kg to 71 kg per ton of waste
• Improved utilization of the resource
• Increased bio-methane production
• Significant reduction in operational costs
• Reduced workload on operators
• Less digestible material to incineration
BioSep® in operation at Ecopro.
Incoming mixed food waste.
Plastic and packaging material as reject after treatment in BioSep®.
History
Ecopro is an AD biogas plant in Verdal, which is located approximately 94 km north of Trondheim. The plant was commissioned in 2008 and the food waste pre-treatment equipment consisted of a drum sieve that was 17 m long and 4 m diameter together with a number of additional processes. The capacity of the drum sieve during operation only treated approximately 2 tonnes of food waste per hour, which was significantly lower than anticipated.
With such low capacity the pre-treatment plant was required to operate 24–7. This resulted in a very high workload for the operators. In addition, in order to maintain operational status, the number of operator interventions required was considered to be very high.
Replacement
In June 2010, Norsk Biogass AS were contracted to replace the drum sieve and install a BioPrePlant® System utilising the unique BioSep® technology for pre-treatment in conjunction with SPIRAC material handling equipment. In early February 2011, a BioPrePlant® System comprising of two first stage BioSep® units and one second stage BioSep® complete with a material feeding and ferrous metal removal systems was commissioned.
It was necessary to install this new equipment alongside the existing plant whilst maintaining plant operation. There were a number of design challenges to be overcome in order to fit the equipment into the existing layout and interface with the existing plant.
Current mode of operation
The new BioPrePlant® System is operating at a capacity of up to 9 tonnes of foodwaste per hour. This has enabled Ecopro to reduce the operating hours to a single eight hour shift per day, seven days per week. Needless to say, this has greatly reduced the workload on the operators, adding to this the BioPrePlant® System is largely self-operated, hence the working environment is greatly improved.
Performance and Production
The old drum sieve mode of operation generated approximately 250 kg reject (mixture of plastics and digestible materials) per 1000 kg of treated food waste. The new BioPrePlant® System has reduced this number to 71 kg per 1 000 kg of food waste. Since the reject from this plant is transported off site for incineration at a cost of € 90 per tonne the installation of the BioPrePlant® System has reduced Ecopro’s cost for incineration significantly. This is estimated to generate a saving of € 300 000 annually.
As the total amount of plastics and packaging material in the incoming food waste has not changed, the reduction of reject volume results from the higher efficiency of the separation process. Ecopro estimate that an additional 180 kg of biomass is passed through to the digesters per tonne of feed stock. This of course means that Ecopro today enjoys higher biogas production per tonne of food waste.
Slurry quality
It is a common concern that slurry produced from food waste contains high levels of impurities such as small pieces of plastics and other particles from food packaging. Norsk Biogass A/S engaged Aquateam A/S to independently test the slurry. The laboratory tests showed that the impurities in the slurry produced at Ecopro are substantially lower than the requirements in most European regulations for utilising the digestate as a bio fertilizer.